The goal is to match the tip shape and size to the contact pad. That allows you to maximize the contact surface area, so you heat the lead and contact area as quickly as possible. If you choose a tip that is too large, you have more tip volume to heat, which will slow down the heat recovery, the time it takes for the tip to reheat after soldering a joint. It also runs the risk of interfering with other components and contact areas. If you choose a tip that is too small, you won’t have enough surface area of the tip in contact with the lead and contact area to transfer heat efficiently. It will take more dwell time, which slows you down and could increase the thermal stress of the component.
Make sure you are using a soldering iron and tips intended for electronic PCB soldering. Tips intended for other applications, like stained glass, plumbing, or heavy electrical work, are generally much larger than what is appropriate for electronics. Soldering tips come in all kinds of shapes to facilitate different PCB geometries: (Have a look to our Plato Soldering tips here)
Pointed or conical
- The end of the soldering tip comes to either a point or around the flat area. The size is specified by the diameter of the end, so can be as small as 0.1mm or larger than 1mm. These tips are generally used when pin-point accuracy is needed, like with very fine leadless surface mount components. They may be long for greater reach in dense board design, or a shorter microtip to reduce the amount of tip metal that needs to be heated. This can improve heat recovery. The ends of the tips may also be bent to avoid interfering with other components or contact areas.
Blade or knife
- A blade tip is usually used for drag soldering when the solder is drawn across multiple contact pads. This is common when soldering surface mount technology (SMT) components. The size is measured along the length of the blade and can be 6.3mm (1/4”) or larger.
Chisel or screwdriver
- A chisel allows you to heat a larger contact area, so useful for thru-hole solder joints. Lengths may vary and can also be bent, like with a conical tip. The size is mainly specified as the length of the flat area, but the depth or thickness of the tip may also vary. These can be so small they almost look like a point, like under 1mm, and as wide as 5 or 6mm.
Bevel
- A beveled tip has a flat oval end set at an angle. Picture a metal rod that is a cross section at an angle. The size is specified by the diameter of the “rod” or shaft and sometimes the angle of the bevel. A bevel can be as small as 1mm or 4mm or larger.
Flow tips
- A flow tip looks similar in design as a beveled tip, but instead of a flat area, it is a little indention or cup. This is also called a “mini-wave tip”, and is commonly used for drag soldering, as explained above.
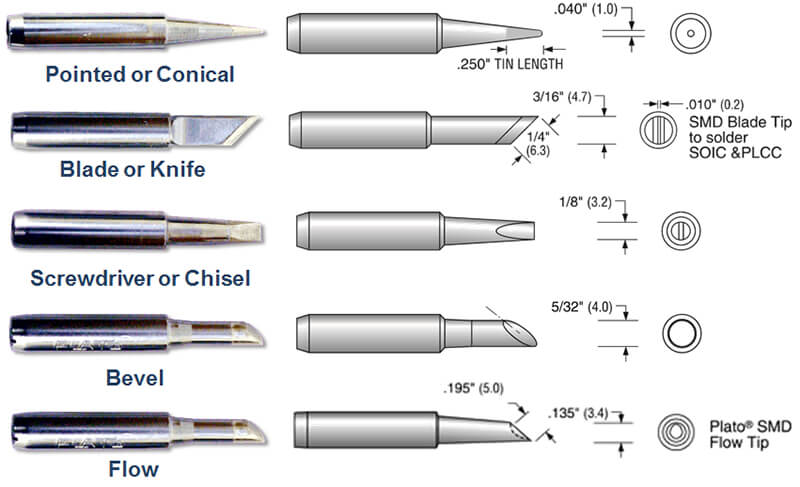