Techspray was approached by a grow light manufacturer that was struggling to produce LED light fixtures with good reliability in harsh conditions. Their solution was to apply conformal coating to their printed circuit board assemblies (PCBA), but that led to a host of complications, which included shutting down their production line for the day due to noxious fumes.
Fine-L-Kote LED2 Conformal Coating was the product that eventually saved the day, but only after rigorous qualification testing.
PROBLEM: HOW TO MAINTAIN LED GROW LIGHT RELIABILITY IN HARSH AGRICULTURAL CONDITIONS
Imagine taking a sensitive electronic device, say your laptop, and placing it in a steam bath. As if that weren’t challenging enough, add caustic, corrosive fertilizing chemicals to the mix. The obvious solution is to coat the electronic assemblies with conformal coating, which is basically a shellac for circuit boards (a bit of an oversimplification, but more details on conformal coating is to follow). The problem is you run the risk that it will dim the light intensity and shift the color, negating years of testing to optimize your light’s performance on plant growth.
Techspray was contacted by a small but well positioned manufacturer of LED grow lights that was attempting to solve those exact problems. Their first choice of conformal coating was naturally from one of the top suppliers of silicone resin. Silicone resin (SR) is the natural choice for coating grow light electronics because it is very hydrophobic (repels water).
From their initial qualification testing, they decided that a thicker than normal cured coating provides them the best overall protection. What wasn’t initially taken into account was the solvent used to thin the silicone resin to a workable consistency.
The competing silicone conformal coating being tested had a high concentration of toluene, which is considered highly toxic and has a very strong odor. When the coating was applied, there were soon a number of complaints of the strong smell and headaches up and down the assembly line. As time went on, it became so disruptive they shut down the production line for the day. Not exactly the best results when time literally equals money!
Before we get into the final solution, how about a little more detail on grow lights in general…
What Are Grow Lights Used For?
Grow lights are electric, artificial light sources used to grow plants when natural sunlight is either not available or does not offer enough control. Grow lights either attempt to mimic the light spectrum of the sun, or the light is fine-tuned in either the spectrum (color) or intensity to achieve specific results.
Grow lights are commonly used for horticulture, indoor gardening, plant propagation, and food production. They are particularly useful for indoor hydroponics. [1]
The Rapidly Growing Grow Light Market
The global market for LED grow lights is rapidly expanding because of booming demand in the indoor farming, commercial greenhouse and vertical farming segments. The legalization of cannabis in many states in the United States and countries around the world has driven much of the increase in indoor farming. In 2020, the market size had an estimated value of $1.28 billion, and is projected to increase to $12.32 billion by 2030. [2]
Major manufacturers of LED grow lights include Black Dog Grow Technologies Inc. (U.S.), Bridgelux Inc. (U.S.), CreeLED Inc. (U.S.), EVERLIGHT Electronics Co. Ltd. (Taiwan), Heliospectra AB (Sweden), Lumigrow Inc. (U.S.), OSRAM GmbH (Germany), Samsung Electronics Co. Ltd. (South Korea), Savant Systems Inc. (U.S.), and Signify Holding (Netherlands). [2]
How Do Grow Lights Work?
Grow lights can utilize a variety of lighting technologies. Initially, incandescent light bulbs were used, with all the disadvantages of lack of control and excess heat. Later generations of lights included fluorescent and high-intensity discharge (HID) lamps. Modern grow lights mainly use light emitting diode (LED) technology common in the electronics industry. [1]
Since individual LEDs usually emit a narrow range of colors, arrays of multiple LEDs are used to either mimic the natural white light of the sun, or shifted in more the red, blue or green direction, depending on the benefits on a specific plant’s grown cycle. LEDs offer a huge value in control, which has led to large advances in productivity of commercial indoor agriculture. Many lighting products consist of a set of LEDs in multiple colors, with electronic controls to shift which LEDs are active, changing the overall color of light produced.
Importance of Light Intensity and Color on Plant Growth
Grow lights are required in indoor farming because plants need light for photosynthesis, to generate energy. Light also affect the way plants grow, e.g. speed and direction, with a process called photomorphogenesis. Photosynthesis generally occurs at 400-700nm on the light spectrum, and photomorphogenesis occurs 260-780nm. [3]
Photoreceptors in plants are activated by varying colors along the light spectrum, impacting growth characteristics like fruiting, rate of grown, root development, plant health, flavor, nutrition, etc. [3] Small changes of as little as 10-20nm in the light color can produce major changes in both plant growth and edible product produced.
One study published in Plants (April 2019) demonstrated that blue and red light can improve growth, color, and antioxidant content in lettuce, spinach, kale, basil and sweet pepper. [4]
Another study published in the Journal of Experimental Botany (April 2017) made the point that the importance of green light should not be overlooked. Green has long been thought to have minor importance in biology because much of it reflects off of plant surfaces (which is why they look green). This research had shown the absorption of green light actually helps stimulate photosynthesis, improving carbon gain and possibly crop yield. [5]
Light intensity from LED grow lights needs to be closely controlled. A 2012 study on light intensity on common sage showed a strong positive correlation of light intensity of the number of leaves, but a negative correlation with the plant’s height and photosynthetic pigments. [6] The optimal intensity will depend on the plant and the most valued characteristics.
Grow Light Reliability Challenges
To manufacture LED grow lights, individual LEDs have to be attached (usually with solder) to a printed circuit board (PCB). In theory, this is a very simple electronic device that should be easy to assemble and be highly reliable. The harsh reality is the extreme environment of indoor agriculture. When you introduce heat, moisture, and caustic, corrosive fertilizer, electronic reliability becomes much more challenging.
Water is naturally conductive, so introducing it to an electronic assembly can create current leakage or short circuit. If there is any ionic residue on the PCBA, like flux residue from the soldering process, moisture and current can lead to dendritic growth. Dendrites are conductive branches that literally grow from one contact point to another, again, leading to current leakage or short circuit. Add corrosive fertilizer to the mix and you can actually break down metal surfaces. At that point, contact pads can lift up and separate, breaking connections, or the metal particles can join and form branches. This is called creep corrosion, and leads (once again) to current leakage or short circuit. For more information, check out https://www.techspray.com/the-essential-guide-to-conformal-coating.
In short, you really need to keep the inner workings of electronic devices clean and dry.
There are several strategies that can be implemented to ensure grow light reliability:
- Sealed packaging / gasketing – All grow lights are packaged with the goal of keeping outside contamination from reaching internal electronics. In reality, it is nearly impossible to keep moisture from working its way in 100% time, and still have a device that is economical to assemble and service.
- Encapsulates (potting compounds) – Another strategy is to fully submerge sensitive electronics into an epoxy resin. That eliminates any possibility of rework or servicing once the PCBA is potted, but it will be water-proof. One concern is the encapsulate over the LED could dim the light and potentially shift the color. It would also make dissipation of heat problematic, which could drastically reduce the life of the LEDs. In LED grow light manufacturing, epoxy encapsulation eliminates the possible of reworking a damaged board or failed LED, which might only require minor repairs. Without the ability to repair, the only alternative is scrapping a complete panel of expensive LEDs.
- Conformal coatings – Rather than submerge the circuit board into a thick layer of resin, a resin layer can be applied that “conforms” to the surfaces of the board and components. Conformal coatings are generally thin enough to allow for adequate thermal dissipation, and unlike encapsulates, they can be removed for rework and repair of the LED grow lights. While not as water-proof as potting compound, conformal coating can provide enough water-resistant protection when used in conjunction with sealed packaging.
Protecting Grow Light PCBAs with Conformal Coating
Conformal coating is a special polymeric film forming product that protects circuit boards, components, and other electronic devices from adverse environmental conditions. These coatings ‘conform’ to inherent irregularities in both the structure and environment of the PCB. They provide increased dielectric resistance, operational integrity, and protection from corrosive atmospheres, humidity, heat, fungus, and airborne contamination such as dirt and dust.
In relation to grow lights, several conformal coating properties rise to the top of the priority list:
- Able to resist moisture and avoid corrosion – Tests should be run to ensure adequate protection to avoid current leakage and corrosion. Salt spray or salt fog testing (e.g. ASTM B117) is commonly used for extreme environment testing.
- Impact on light intensity and color – If the conformal coating is applies around the LED surfaces, it will not have any impact on light transmission. Unfortunately, this either adds a laborious masking step to the coating application process, or requires a selective spraying process. In addition, each break in the coating is a potential failure point where moisture and other contamination can enter. It is possible to coat over the entire PCBA, including the LEDs, but optical clarity of the coating needs to be taken into account. Otherwise, there is a risk that the light intensity is reduced or color shifted, potentially hindering optimal plant growth.
- Compatibility with components – Incompatible chemicals in LED lighting assemblies can hurt performance and reduce service life. Modern LEDs often contain unique silicone polymers that are optically clear, thermally stable, resistant to UV exposure, and economical. An incompatible chemical can diffuse into the silicone lens or outgas, causing discoloration and shifting of the transmitted light [7].
- Toxicity – The reliability of the equipment is important, but equally important is the safety of those in the PCBA assembly operation. Conformal coating resins are often dissolved in or blended with harsh and toxic solvents like toluene, xylene, and methyl ethyl ketone (MEK). All three solvents are on the US list of Hazardous Air Pollutants (HAPs) and have been shown, with enough exposure, to lead to a number of negative health effects like cancer, liver damage, and renal failure.
Conformal coatings generally contain either acrylic resin (AR), silicone resin (SR), or urethane resin (UR). Engineers specify the type of coating depending on the environmental issues that need to be mitigated. In the case of grow lights, silicone-based conformal coatings are ideal because they are hydrophobic (repel water), have good chemical resistance (i.e. against caustic fertilizers), do not yellow over time (shifting color being transmitted), and generally have a higher heat tolerance compared to other coating types.
Customer Solution: Fine-L-Kote™ LED2
After restarting their grow light assembly line, the project managers were very determined to find a conformal coating that meets all their performance criteria, but without the noxious chemicals. Luckily Techspray was able to offer an ideal solution off-the-shelf, Fine-L-Kote LED2 (part #2125).
Techspray Fine-L-Kote LED2 is specifically designed and formulated for light emitting diode applications, where a completely transparent coating is required to provide a tough, extremely flexible protective coating. Fine-L-Kote LED2 provides highest flexibility for extreme temperatures on the flex and rigid circuitry found on LED displays, and provides an outstanding non-stick surface for soil repellency.
Cured coatings are hydrolytically stable and retain their physical electrical properties after high temperature and humidity exposure, without interfering with light wavelength or intensity. Fine-L-Kote LED2 will not stress delicate components.
Fine-L-Kote LED2 does not contain HAPs like toluene, xylene, or MEK, so it is much safer on personnel.
Of course marketing bullet points are great, but qualification testing was required to ensure the reliability of their grow lights were improved without affecting light transmission:
- General coating performance (IPC-CC-830B)
IPC-CC-830B is a battery of tests, some are pass-fail and others provide data that can be referenced and compared. Qualifications include coating appearance, insulation resistance, fungus resistance, flexibility, flammability, moisture and insulation resistance, thermal shock, and hydrolytic stability. Fine-L-Kote LED2 passed all of the above qualifications. UV fluorescence is normally included in IPC-CC-830B, but is not applicable for this particular coating. UV brightener, which glows under a black light, is often added to conformal coating formulas to aid QC inspection. Techspray did not include UV indicator in Fine-L-Kote LED2 because of the potential of negatively impacting light transmission across all spectrum including ultraviolet. The UV indicator absorbs the invisible UV light and re-emits it at a longer wavelength in the visible range, allowing you to see it for quality control inspection. So, if a plant benefits from a specific wavelength of UV light, a UV indicator could negate that benefit.
- Optical clarity (IESNA LM-79-2008 and ANSI NEMA ANSLG C78.377:2015)
Fine-L-Kote LED2 was shown to have almost no impact on either intensity or color (see diagram below).
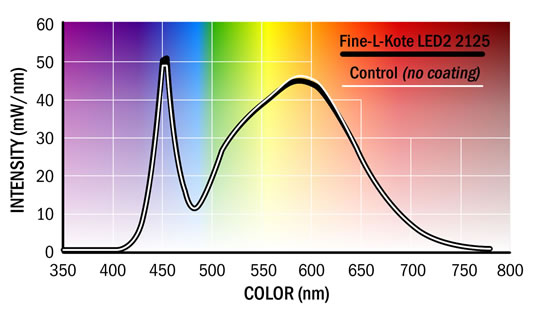
- Corrosion protection (MIL-STD 810G)
Accelerated corrosion testing enables manufacturers to evaluate new coatings in a controlled environment. This avoids learning about reliability issues the hard way -- from field failures. LED fixtures were run in a salt fog chamber with a standard 5% NaCl solution for several weeks. LED performance was measured before and after the test and compared, looking for signs of degradation. Fine-L-Kote LED2 was able to withstand this extreme test of corrosion resistance.
- Chemical compatibility (Cree qualification)
The LEDs are attached to a PCB, coated, connected to a power supply, and the test is run for at least 6 weeks (1000 hours). Fine-L-Kote LED2 passed the Cree compatibility test for all LED components and is listed on the Cree XLamp LEDs Chemical Compatibility guide (CLD-AP63 Rev 6A Aug 2018). [7]
In addition to meeting all of their required specifications, Fine-L-Kote LED2 was able to vastly improve their production throughput. The conformal coating that was previously qualified and used forced them to apply two coats to achieve the desired thickness. Fine-L-Kote LED2 was able to achieve the same thickness with only one pass.
Conclusion
After 1-2 years of qualification testing and logistical work, Techspray Fine-L-Kote LED2 is improving reliability of tens of thousands of grow lights per month, including those in the US, Mexico, and Asia.
Opportunities abound in the grow light markets, but competition is fierce, so product quality and reliability is critical to success. Techspray Fine-L-Kote LED2 is a proven competitive advantage for grow light manufacturers, allowing their products to withstand the harsh indoor farming environment and continue to optimize agricultural output.
For more information, contact a Techspray application specialist at 678-972-1853, tsales@techspray.com, or to go www.techspray.com.
References:
[1] https://en.wikipedia.org/wiki/Grow_light
[2] Allied Market Research, “LED Grow Lights Market By Wattage (Low Power, Medium Power, and High Power), Spectrum (Narrow and Broad), Installation Type (New Installation and Retrofit), and Application (Indoor Farming, Commercial Greenhouse, Vertical Farming, Turf and Landscaping, Research, and Others): Global Opportunity Analysis and Industry Forecast, 2021–2030”.
[3] Limigrow, Nov. 19, 2019 blog “The Definitive Guide to Grow Light Spectrum”.
[4] Plants (Basel), 2019 April 8(4): 93, “Blue Light added with Red LEDs Enhance Growth Characteristics, Pigments Content, and Antioxidant Capacity in Lettuce, Spinach, Kale, Basil, and Sweet Pepper in a Controlled Environment”.
[5] Journal of Experimental Botany, Volume 68, Issue 9, 1 April 2017, Pages 2099–2110, “Don’t ignore the green light: exploring diverse roles in plant processes”.
[6] Biological and Applied Sciences, Feb 2012, by George Zervoudakis, “influence of Light Intensity on Growth and Physiological Characteristics of Common Sage”.
[7] Cree, Aug 2018, “Cree XLamp LEDs Chemical Compatibility”.